About Us
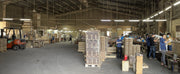
Since 2018, innovation, quality, functionality, and durability have been at the foundation of the Cozifa brand. All Cozifa products are designed and manufactured at a 5,000 square-foot facility in VietNam

" Best purchase I’ve made this winter! The color and knitting are exquisite and it's so comfy! Went from NYC to Miami without ever taking it off. Super cute!! "
Cozifa's History

The trio of owners/entrepreneurs created cutting boards as gifts, and Cozifa was born in 2018. Our cutting board manufacturing facility is a reliable production base specializing in the production of high-quality cutting boards. With over 10 years of experience in the food production industry, we take pride in providing the best cutting board products to meet our customers' needs.

Made in Viet nam
All Cozifa products are designed and manufactured at a 5,000 square-foot facility in VietNam. Our factory utilizes advanced manufacturing equipment and modern production processes to ensure the quality and precision of each product. Our experienced team of staff is dedicated to meeting customer requirements and committed to producing high-quality products on time.
Be proud to know that Cozifa products help support a commitment to sustainability, a safe and ethical working environment, and high-quality products

Lumber
Production begins with the purchase of wood logs. Wood logs are thick planks made by cutting a section of wood into similar thick planks.
Typically, we purchase green wood logs with a moisture content of 60-80%.
Before production starts, the green wood logs are air-dried for a minimum of 6 months. Natural air drying allows the wood to stabilize in terms of strength and hardness, making it less susceptible to size changes in the finished product
Specifically, American walnut wood is imported directly from the America. Made from natural North America Walnut wood, this meat block is perfect for cutting, chopping, slicing, and serving food. Its strong, dense, and sturdy structure allows it to resist moisture, shock, deformation, and mechanical damage.
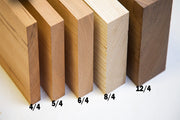
Picking right wood to the product
The key is to choose the right thickness and quality of material to suit the product.
Selecting the right material allows us to minimize wood waste during production.
We consider responsible wood management as our ecological duty.
There should be no waste.
The standard thicknesses of the product are: 20 mm - 30 mm - 40 mm
However, there's no issue with producing products in different thicknesses if requested by the customer
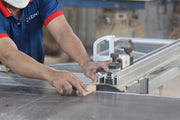
Cutting
Now is the time to determine the thickness of the final product. If we plan to produce a cutting board with a thickness of 20mm, we need to cut the wood into boards that are 28mm thick (2mm for planing inside the drying chamber and the remaining part for thickness and sanding)
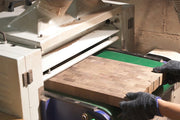
Four side planning
The cutting boards are glued together from multiple wood strips.
To achieve perfect quality of the laminated sheets, it's necessary to have a perfectly straight surface.
A four-sided planer creates thin, straight sheets on all four sides, giving them a perfect rectangular shape. This condition is mandatory to continue production.
The width of the sheets used for the cutting boards ranges from 40-60 mm. But 20 mm can also be used. The width of the lamellas depends on the actual available material
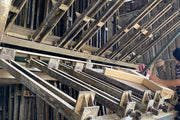
Gluing process
The perfectly designed thin sheets are glued together using special adhesive. The type of adhesive we use is water-based and certified as safe for food contact.
Wood comes in a variety of colors. The color of wood can vary depending on the type of cutting board.
The color of a wood product depends on:
- The type of wood
- Where the tree was grown
- The time the tree was cut (winter-cut wood tends to be lighter, summer-cut wood tends to be darker)
- Which part of the wood the lamella is made from (the core of the wood may be darker, such as walnut, while the outer part may be lighter)
- The finish (after applying oil or varnish, the wood may appear darker)
The challenge is to match the color of the thin sheets at the laminating stage. It may take a little more time and effort, but in practice, perfectly matching thin sheets on the cutting board will yield excellent result
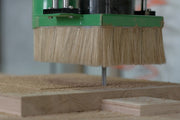
CNC– Machines
A Computer Numerical Control (CNC) machine has the ability to produce a wide range of products and various types of manufacturing tasks based on numerical and geometric commands, alow to produce almost any shape of the cutting.
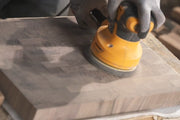
Sanding–Making the sides
This is what you should imagine when getting a good end product. It took us some time to figure out how to create this effect, and the solution was simple, as usual: try harder and make it better
PACKING TO UNIT BOXES

Our factory utilizes advanced manufacturing equipment and modern production processes to ensure the quality and precision of each product. Our experienced team of staff is dedicated to meeting customer requirements and committed to producing high-quality products on time.We guarantee that our cutting board products are made from the finest and healthiest materials, with a variety of sizes and styles to meet every customer’s needs. We have established the Cozifa brand to provide consumers with more choices and offer the best products and excellent customer service. We aspire to become your reliable manufacturing partner.
Our Team
Passionate About the Product,
Committed to the Community

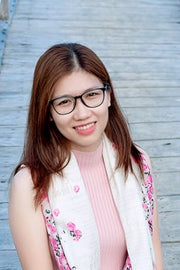

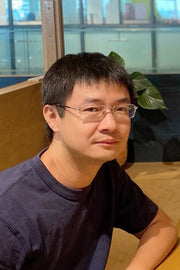
What People Say
TESTIMONIALS
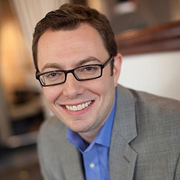
This Cozifa End Grain Walnut butcher block cutting board is very well made and looks great. The color is very dark and looks very high-end. It came well sanded and oiled and water just beaded up on it. I’ve been using the cutting board for several weeks now and am very impressed with it, especially for the price point. I definitely recommend it.
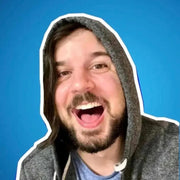
The Cozifa End Grain Walnut Wood Cutting Board has become the go-to tool in our busy kitchen. Its generous size and durable construction make it perfect for all our chopping and slicing needs. The juice groove prevents messes, and the inner handles allow for easy maneuvering. The beautiful finish with beeswax, linseed, and lemon oil adds an elegant touch to our countertop, and the included gift box packaging makes it an excellent gift option for any cooking enthusiast. It’s a must-have kitchen essential for any family.
Kyle Istook
Newyork
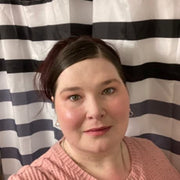
This cutting board is a work of art. The craftsmanship is impeccable, and I can use it over top of my sink to add counter space in my tiny kitchen. I use it every day and it looks great in my kitchen.
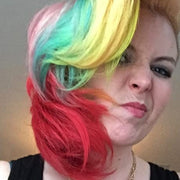
Add customer reviews and testimonials to showcase your store’s happy customers.